Performance Evaluation
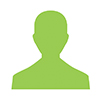
The plant manager of a small manufacturing company showed me a performance evaluation form he developed for plant employees. Assuming these performance criteria are related to a job analysis, would any of these appear vague or ambiguous (which, of course, could cause the company difficutly in the presence of disparate impact)? He plans to use the following scale throughout:
Unacceptable 0 1 2 3 4 5 Excellent
THe performance criteria are: Punctuality, Absenteeism, Quantity of Work/Productivity, Quality of Work, Follows Instructions, Works well with others, Sanitation (keeps work area clean and tidy), Personal Hygine (the plant is in the food industry and must meet certain standards with regard to plany and employee cleanliness).
He plans to evaluate employees quarterly, and based on their cumulative points at the end of the year determine their raises in this manner...
0-96 points=not eligible for a raise at this time, 97-120 points=eligible for a cost of living raise, 121-140points=eligible for an incentive raise (added to base pay). 141-160 points=eligible for a lump-sum bonus (in addition to the incentive raise, but not added to base pay).
I'd appreciate any comments/suggestions. Thanks.
Comments
I would provide a label for each element of the scale rather than just anchors. I would eliminate "0" from the choice list. If using an even numbered scale, consider reducing to 4: the point is to force a choice and eliminate a neutral response. The more numbers you have available, the more "neutral" the effect of the center 2.
Some of these things are actually measurable. Instead of "punctuality" consider "lost minutes due to short shifts" and use actual payroll information. Similarly so with "absenteeism" consider "days absent but not job protected (e.g., FMLA)". You run the risk of a supervisor giving different scores to people with the same lost time without simply referring to the numbers. With a set standard, these things can be 100% fair across the board. The standards can differ in some cases (e.g., stricter attendance standards on critical production equipment than on uncritical equipment as long as employees are aware of their own standards).
If you have a formal QC/QA department, then you can have quantified quality information. Quantity of work is a simple production count.
I would say that most of the items are countable from your own records and should not be left up to someone trying to circle some numbers to get a sheet of their desk.