Safety Incentive Programs - Any Ideas?
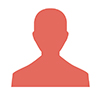
I am trying to find Safety Incentive Programs to review. We are looking to implement a Safety Incentive Program for our construction crews that use quarterly incentives.
Thanks!
Thanks!
Comments
In the past, when I worked in the manufacturing industry, we would do things like buy lunch for the shift that had 0 accidents/near misses each quarter, give something to the person that reported a potentially unsafe condition, etc.
One thing to consider about Safety Incentives, is that they sometimes have the opposite result. You want your employees to report any accidents/near misses immediately so that you can correct the situation and make sure it doesn't happen again. If you have an incentive for the team that has 0 accidents/near misses then someone may not report an injury just so they are not the person that ruins the streak for everyone else. We actually stopped the lunch each quarter because of this. We found out that someone had not reported something they should have because they didn't want to ruin lunch for everyone else.
Some other things we did to promote safety:
ITHR is right--peer pressure NOT to report is extreme, especially if the incentive is a good one. That's why we dropped our program (through an outside vendor). We did keep the big flip calendar of days without lost time.
I like the idea of the Safety Day and luncheon! May run this by upper management.
We have tried for years to run without a safety incentive program, and every year, our number of 'preventable' accidents rises - in this year alone, we have had one every week. We are going to try this route and see if the employees begin to take to heart paying attention - documentation, investigation and going through and explaining how to prevent the accidents have all been played out here.
If anyone has a Safety Incentive Program in place, I would appreciate the ideas.
Thanks!
I can recall a time when we simply fired someone for failing to lock out / tag out.
Do you know if your safety procedures are being followed? Sometimes I think we go too far in paying people to do the right thing in the first place and not enough in raising our level of expectation in common sense. This is similar to the debate about attendance bonuses. Aren't people supposed to show up at work?
[quote user="TLCTX"]I have tried that route, and the superintendents constantly fail to follow through, with no consequence. The only one who can change that mindset here is the owner of the company, and his idea is to create a Safety Incentive Plan, which is why I am asking.[/quote]
This is one of the maddening things about HR. It's role, purpose, and power structure varies quite a bit across companies.
Do you have any direct authority in disciplinary matters? If not, this is a tough place to go. Is there a safety officer? If so, is that person in HR? Do they have any authority? Supervisors that live in a culture where enforcement of company policy is not part of their job create a lot of trouble. That's a cultural change that just takes a long time.
Try selling your boss on the problems with safety bonuses. Explain how they can get employees to subvert the system by encouraging them not to report injuries. Explain how it is similar to an attendance bonus (unless he really loves those). In the end, paying people to do their job and do it correctly once trained appropriately should be the standard in my opinion. If you have a typical, "modern" employee handbook, there's probably a code of conduct but none of that means anything if, in your employee relations role, you have no disciplinary authority.
The owner figures this may help our Safety Issue out, and I have no choice. I also have to have the program completed and ready for implementation by Monday 6am.
Ok couple of questions for you. If you are not being notified of the accidents/injuries, who is completing the OSHA log? Who is taking the employee to the doctor and monitoring the WC cases to ensure that the employee is following doctors orders and returning to work when they are supposed to?
Not having all of the facts, here is what I would do. I would put a Safety Plan together that includes a Safety Incentive program as part of this plan.
In order to be successful, I think your plan needs to have a number of different things.
1. Safety Policy -
2. Safety Committee - Should include you, the Supt, and numerous employees from different departments or job duties. This committee reviews all accidents, make recommendations on how to prevent this from happening again, discuss safety topics to go over with all the employees. You should meet once a month.
3. Safety Banner - If you can find a sign shop that can do this really quickly, get a banner made up that says "Safety First". Make it big enough and on material that everyone can use a sharpie to sign it. By signing this they are committing to also doing the job with safety in mind.
4. Safety Day - Once a year, pick a day to go over Safety. Things to do during this day:
* Review your safety policy. Have everyone sign a new Safety First Banner. Provide lunch for everyone. Have some contests and give out prizes like gift certificates to resturants, fast food, Target, Wal-Mart, gas cards, etc. We had a contest to see who could guess the total number of fire extinguishers we had in one of our plants. If you give out safety equipment like hard hats, gloves, boots, etc. use this day to give out new onese to people.
Somehow my message posted before I was finished. Let's try this again...
Ok couple of questions for you. If you are not being notified of the accidents/injuries, who is completing the OSHA log? Who is taking the employee to the doctor and monitoring the WC cases to ensure that the employee is following doctors orders and returning to work when they are supposed to?
Not having all of the facts, here is what I would do. I would put a Safety Plan together that includes a Safety Incentive program as part of this plan.
In order to be successful, I think your plan needs to have a number of different things:
1. Safety Policy - This should be a company statement about policy. This statement should be posted at every worksite and in every department. Along with this policy you should have safety rules that include how and when an accident/near miss should be reported, what to do if someone is injured, who to go to if an employee sees a potentially unsafe condition, etc.
2. Safety Committee - Should include you, the Supt, and numerous employees from different departments or job duties. This committee reviews all accidents, make recommendations on how to prevent this from happening again, discuss safety topics to go over with all the employees. You should meet once a month.
3. Safety Banner - If you can find a sign shop that can do this really quickly, get a banner made up that says "Safety First". Make it big enough and on material that everyone can use a sharpie to sign it. By signing this they are committing to also doing the job with safety in mind.
4. Safety Day - Once a year, pick a day to go over Safety. If you can make this happen I would schedule this day in the next couple of weeks. Things to do during this day:
* Review your safety policy. * Have everyone sign a new Safety First Banner. * Provide lunch for everyone. * Have some contests and give out prizes like gift certificates to resturants, fast food, Target, Wal-Mart, gas cards, etc. We had a contest to see who could guess the total number of fire extinguishers we had in one of our plants. * If you give out safety equipment like hard hats, gloves, boots, etc. use this day to give out new onese to people. * Have forms available for people to fill out and report potential safety hazards * Have a contest to see who can come up with ideas to make the workplace better. Give everyone that submits a good idea a prize.
5. Post the number of days each location/department/team/etc. has gone without an accident/injury.
6. Have a contest to see how many locations/departments/teams/etc. go a month, then a quarter, then 6 months, then 1 year without an accident/injury. For each of these threshold give away something that is important to them. It could be free lunch, gift certicates (free gas maybe?), free products (maybe new work boots or work clothes), etc.
7. Lastly and this is probably going to be the most difficult part is that you need to have a discussion with both partners in the company, when you present this plan. In order for this safety plan to work, if you are going to be doing all the work for the safety issues, you need to be notified and involved in all aspects of safety. Tell them that you are willing to help make this work but you need their support for it to work as well. That includes being notified of accidents so that you can take care of the paperwork like workers comp and OSHA logs. Hence why I asked who was doing the log. What is the fine for logs not completed? Thousands and thousands of dollars. You can do a google search and see all the articles about OSHA doing random inspections, especially construction sites, as they have said construction is one of their targets this year. If you are not the one taking care of the WC issue, then tell them you will take over this aspect. This could potentially save the company thousands of dollars. Make sure the employees are going to the company doctor (as long as your state allows this) and then following the orders. Have the doctor come visit your location and talk about what options the company has for light duty. I can't tell you how many times employees told our doctor that there was no light duty available but all of the doctors we sent our employees to knew what the light duty assignments were b/c we had them visit our operation. If there was a question, they would call us to get clarification on light duty. In my past life I monitored all the WC cases and made sure that employees returned to duty when they were supposed to.
Also you need their assistance to institute a safety disciplinary policy. Tell the owners that you will help them with the documentation and disciplinary action, but in order to make this work you need both reward and discipline. As much as the discipline should be on the manager to handle, I have seen it work that if you offer to help them with the documentation and disciplinary action then it will get done and then become a practice. You also need the owners help to pass this message on to the other supt.
This is one of those times that you need to have a tough conversation as the HR professional.
If you send me your email address I can send you some of the forms I used in the past for some of these contests, etc. that I have talked about so that you don't have to recreate the wheel.
I hope this all makes sense to you. I was thinking about all of this as I was typing and I was going in so many different directions that I wanted to make sure I got it all down for you.
Addressing the political issue, you may want to take the owner aside and let him know what he's in for if the Company continues down the road of undocumented lost time accidents.
Here a zinger. "If supervisors don't have to report lost time accidents, then why would we believe that they would report illegal harassment?" Then tell him what happens when supervisors know but do nothing.
I'm sympathetic to your situation and I hope you can come up with something on time. I suggest the award be team based rather than individually based. Safety is often a group effort. Maybe start out with a bank of money for everyone to divide up and deduct based on the frequency and/or severity of accidents with a multiplier for preventability.
Thanks - I instilled a new safety policy about a year ago, with documentation on accidents and a deadline for accident reports, and accountability for those that failed to follow - I had all the bells and whistles. The problem is that the superintendent/partner doesn't feel that all accidents are necessary to report to the office. I get timely reports in on injury related accidents - what I do not receive are the accident reports where we damage utility lines, company vehicles, etc, and I try to explain that all those incidents are just as important to our bottom line, and that those are the type of incidents where our foreman can easily be found at fault, and documented for their missteps - but I do all this to deaf ears.
I have even written foremen up for screwing up, and sent them to get disciplined and sign, and never get them back.
Your ideas are appreciated. Thanks for all the time you put into it. I am spending the next two days on this, and hope to come up with something.
My email address is vmartinez@levycompany.com - any help is appreciated.
Have a great weekend - Vanessa
Vanessa - I sent you 8 documents via email. Let me know if you didn't get them.
I teach at Saint Joseph's University in Philadelphia in a Masters level program in Envoronmental H&S. I have an unpublished article that lays out some basic considerations for a Safety Incentive Plan.
Send me a requesting email FMielke@audubonconsultants.com and I'll be glad to share with you - no obligations.
Frank
I have worked with both large national companies and small local companies, and what everyone is saying is true, the tendency to "not report" is huge, especially when bonuses are on the line. I took over the safety program for a circuit board mfg who was spending $700 per month on first aid supplies, yet had no reportable accidents. It turns out that the safety supply company sold them a "bill of goods" and advised them to carry an enormous supply of first aid items, even those not associated with potential injuries at the location. The items ended up walking out the door with employees. I cut out 90% of the supplies and locked the cabinets, providing only managers and leads with the keys. Anything removed from the cabinet had to be signed out, including bandaids. To enforce this, I walked the locations every day and monitored the boxes. the word got around that someone was actually interested in safety and watching. Things straightened out, incidents were reported because they would eventually come out once the cabinets were opened and reviewed. The supervisors were rewarded for reporting incidents without having to be asked.
Another idea that I have used to convey the attitude of reporting was to instill this within the training. The "students" are required to point out all the mistakes that I make while the training is conducted, and even awarded "I prevented an injury" button when they prevent injuries. It becomes a sense of pride an accomplishment, not a negative. Go after the upper mgmt with that attitude and you mighy have more success.
Our safety committee is looking for incentive program ideas. Would you be able to send me some of the documents you forwarded to Vanessa? I am at our corporate offices. We haven't had any reportable injuries for several years but want people to continue to be safety conscious. Have you had good experience with your incentive program?
Thank you!
Renee