Overtime vs. Additional Hire Calculation
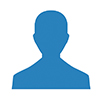
I've been charged with Mission Impossible. We are an auto supplier located in Mich. We are non-union. I've been asked to develop a calculation to assist in determining whether overtime is appropriate or hire additional employees for production operators. I know, it depends. But, recently I read (somewhere) an article with a calculator in it regarding this process. Can anyone give me some guidance ASAP. Thanks so much.
Comments
This indicated to me me they should just hire one or two more employees for afternoon shifts to get the opening shift folks out of there. The OT was being paid to people who came in at 6AM and "got stuck" staying late regularly.
Hope this helps!
There are certainly other factors one should consider when adding an employee. Some of these costs come with a new employee that would not be incurred again with an existing EE.
Health insurance and other employee paid benefits that do not vary with each dollar of the paycheck are a couple of examples. These expenses are already "sunk" into the cost of the existing EE but have to be incurred all over again with the new employee. Other "soft" costs, such as the administrative burden of adding an employee to the system, providing required trainings and orientation are also new costs that an existing employee does not require.
There are different kinds of investments required with different kinds of new employees. For example, an office employee may require another desk, chair, calculator, computer, telephone, etc. and these may cause some back office charges such as expanding licensing agreements, or increased switchboard capacity for a new telephone and other hidden costs.
A warehouse guy may need tools, and a line production worker will have similar kinds of investments to make and a space in which to work. I am not familiar enough with this environment to come up with many examples, but I am certain others have good examples.