Compressed Work Weeks
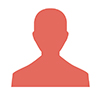
I have been trying to research the impact of compressed work weeks (four ten-hour day) on a manufacturing operation. Other than a few statements, most of the material I found pertained to office or retail operations. Does anyone out there know of a source for this information. We are trying to convince top management that the 4/10 plant operation is not a good idea (increased msd's, reduced efficiency) and I would like something solid to back it up.
Any ideas would be greatly appreciated. xpray
Any ideas would be greatly appreciated. xpray
Comments
I know that this wasn't what you wanted to hear but it turned out to be a good thing.
(Their normal hours were 7:00a. - 3:00p. and 3:00p. - 11:00p.)
We found efficiencies to be better during the summer hours and did not experience an increase in accidents/incidents.
The efficiencies were so much better that we approached the direct labor with the idea of extending the hours beyond the summer. They wanted no part of it. They stated it was nice to do for a little while during the nice weather, but it's not something they would want to have to do during the dead of winter.
Margaret Morford
theHRedge
615-371-8200
[email]mmorford@mleesmith.com[/email]
[url]http://www.thehredge.net[/url]
Experience among my clients, and what I remember of the research, is in line with the comments above -- i.e., the 4/10 schedule is often well-received and provides improved efficiencies.
HOWEVER, note that in some states (at least here in CA) there are laws that go beyond FLSA, and require overtime pay after 8 hours in a day. This cost can be avoided, but it requires a secret ballot and other measures you should examine closely before proceeding.
Regards,
Steve
Steve McElfresh, PhD
Principal
HR Futures
408.605.1870
Have you examined the jobs in the department that are causing carpal tunnel? Could it be the nature of the work, or lack of training, and not the schedule that is actually causing the accidents and injuries?
You should look into implementing proper ergonomics or alternative work methods, possibly cross train employees into other jobs or provide additional breaks in order to reduce the stress placed on the hands and wrists.
Its sounds to me like there is something more than the 10 hour days going on that needs to be looked into.
Do the analysis and talk to the employees, you may be surprised as to what you find.
Good luck!
Oh, I must add, our plant has worked 617 days without a lost time accident.
The book Human Resource Management devotes a little information to accident rates and work schedules. It points out that fatigue based accidents on physical factors rarely exists in today's industry, but accidents caused by boredome (doing the same tasks for a long period of time) is rather common.
Hope this helps.
We have done job analysis, have engineered in some significant work cell changes and do use job rotation, but we may need to do more. I believe it's time to call the Corporate EH&S person back in.
We also have at least one CTS case that our doctor (and suspicious me)think may have been "caught." ((We are investigating.)
Thanks again.
xpray