Safety Meetings
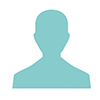
I have recently been put in charge of organizing and preparing our company safety meetings. I do not know the first thing about safety issues. Could someone give me some help or give me a website where I could get some information. They are telling me we have to have safety meetings once a month and that there are certain things that have to be covered. More and more our safety program is becoming my responsibility and I'm afraid I'm at a loss at what to do.
Comments
First, I would check out OSHA's website [url]www.osha.org[/url] for some basic background information - and what you need to cover because if varies depending on whether you're in general industry or construction, health care, etc. I would also recommend checking out the JJ Keller series of software, which I use to prepare my trainings - they have Safety Plan Customizer, Safety Training Customizer and Safety Audit Customizer. Really good information, but the interface isn't really user friendly, so it takes some time to work around it. Good luck.
I hope this helps.
For our safety meetings, we do a monthly safety inspection. We ask for volunteers and get office personnel, maintenance mechanics, engineers, lift truck operators, etc.. Different eyes see different things. We also instruct them that if the issue is important deal with it on the spot. We don't want them to come to the safety meeting and say last week we saw sparks shooting out of a machine and someone should look at it. We talk about the inspection and dole out responsibilies to fix things. Then we review our accidents and determine causes and follow-up actions. Then we let people talk about safety issues. We stress that we don't want to hear complaints without some solutions. They used to throw out problems to mgmt and runaway. Not anymore. The other issue you will have is participation. If you run it like it's a meeting that you have to do and can't wait for it to be over, it will go nowhere. Make it meaningful. Donuts or breakfast biscuits don't hurt either. Good luck.
Try this link and it will take you to some resources for safety info. I know there are a few items for sale on this site and I want to make it clear I am not selling anything.
[url]http://www.emeetingplace.com/programs/safety_files/safety_talks.htm[/url]
Safety is a personal choice and in any organization it has to come from the top down. If you don't already have a good safety culture in the workplace you have your work cut out for yourself. I hope your leadership team is behind the process and not just giving a safety program lip service. Remember, if you talk the talk you must walk the walk. Don't violate any safety rules that are in place and if there are no safety rules that can be on your first order of business as a safety team, if you form one.
We are a manufacturing environment and all of our safety rules were developed by first doing a hazard analysis on each position in the mix. Our hourly ee's developed the safety rules and that helps in the ee buy-in of the safety program.
If I may, we have worked for 413 days since our last OSHA recordable event and over 1.7 million manhours since our last loss time accident. Our workforce is proud of this accomplishment and we reward them for their safety efforts every 75 days.
Don't forget to check your state web site, the National Safety Council, American Society for Safety Engineers, OSHA, and, well, you probably get the picture, as stated earlier there are plenty of sites available for safety info. Hope this helps and good luck.
[email]tcolson@oldcastleglass.com[/email]
Tammy
A good site to check out as well is BLR (business and legal reports) they have a lot of pamphlets and brochures that talk about safety and proper techniques around electricity, chemicals, PPE, lifting, CPR, etc.
If you don't know where to begin, you should consider taking an OSHA compliance seminar. Pagent Thomas or Natsem.com offers them all over the country.
My suggestion, form a committee, get ee's involved and delegate research and work so that ee's take a sence of ownership in their safety.
I contacted our workers comp group and had them send a safety inspector and did a thorough inspection. The service is free and they sent someone who specialized in our industry. She had a ton of suggestions as to how to go forward with safety meetings. Depending on your company you might meet some resistance to the amount of changes that will have to be done to be compeletly safety compliant. It's very expensive if you already have safety issues and sometimes management doesn't realize that.My former company looked at the report and tucked it into a drawer and promptly ignored it, this was AFTER one of their locations had just had an OSHA inspection.
xflash
Good Luck, I hope you have a company leadership which is pro-active Safety, otherwise, in a lot of cases it is a losing situation.
PORK
In reponse to a previous question, the "they" I am refering too is the Vice President, the Director of Operations and the Plant Manager.
Ditto what FHR said. We have a great program here in TX called OSHCON, through the TX W/C commission. It is free and a tremendous resource. There are 3 Gainesvilles in TX so I don't know what major city you are close to. This is the San Antonio contact info and if they aren't the closest office, they can refer you.
John A. (Al) Chadwick
Texas Workers' Compensation Commission
9514 Console Dr., Suite 200
San Antonio, TX 78229-2043
210-593-0070 x 704
[email]john.chadwick@twcc.state.tx.us[/email]
Good Luck!
You could call in OSHA for a voluntary inspection but I would think long and hard before doing so.
The OSHA website will help you but some mandatory training areas for mfg. are Hazard Communication, Lock-Out/Tag Out, Confined Spaces, Emergency Response. Hazcom is the biggie though - every OSHA inspect checks for this.
Good luck - safety can be a two-headed monster but you can tame it.
regs, noise levels and air quality. Personally,
I would not invite OSHA in on a voluntary inspection. They are considerably more helpful now than in the past, but they still have a job to do and you are just getting your program in line.
Welcome to the World of Safety. Here are my assumptions based on your post: The safety program at your company is either new or poorly run (which you'll change) and that currently, there's not a lot of value placed on this program (especiallyif they would hand over the reins without giving you guidance to proceed). Also, I would say your company is small, hence the issues of safety are put in HR's lap as opposed to hiring an actual safety manager. Okay, been there, done that. Now turn them on their ears.
From my standpoint on safety you have to cover three broad categories: Administration, Evaluation & Leadership.
Under Administration, you have to get your paperwork/procedures together (paperwork/procedures is broad - forms for lock-out/tag-out, MSDS, Safety Committe minutes, hearing prevention, etc.). This means starting from scratch or reviewing materials that are already in existence in your company. Fortunately for you, you don't have to worry about additional state laws - OSHA (the federal standard) is king (or queen x;-)). So, I'm including the Texas Worker's Compensation Commission website: [url]http://twcc.state.tx.us/[/url] On this site, you will find helpful links to OSHA as well as a resource link that will help you put together your administrative policies/procedures & forms.
Next, Evaluate. This site also offers training times & free educational videos - what the heck - take the training sessions & watch the videos. FHR had excellent advice & it turns out, the TWCC will come out for free to inspect - have them come out & take notes. Once they come out and your behind the scenes training is over - then go out onto the floor for the purpose of safety (I'm sure you go out more than that, but this is specific to safety). Write up the issues you see, talk with the ee's & find out what their concerns are - evaluate what the issues are and write them down. Which will lead you to the last category, Leadership.
It's up to you to determine what type of Leadership you will display in this area. There's many methods, but for me, I would take the position that safety matters, people matter & safe people = greater profits to the company in the form of higher morale, lower industrial insurance premium costs, lower turnover, less time away from work due to injuries, etc. By addressing safety from this standpoint to the management at your company - you stand a better chance of getting their support - it's dollars and cents. Through this type of Leadership - you will get results which equals compliance. Compliance is very important - ultimately it's the most important thing - but you can't get it without Leadership. And to the last word on Leadership. You have to get management on your side about safety & it needs to be upper management. In this job you will face managers/supervisors that balk at anything new getting introduced & you will need to have upper management in your back pocket to over rule their objections.
Long email - many other issues - I wish you well & hope that you take this job on with vigorous intensity!
First hand knowledge counts for alot.
HR folk typically hate to do this, but leadership requires action...at many levels.
An HR weenie would never hit the floor and put his / her hands on the process. HR weenies are thrilled to administer.
Your organization will LOVE this. If you do decide to do this, make sure you don't get hurt in the process.
If your workers' comp insurer offers risk management consultation, go there first. As another poster said, they don't issue fines for violations.