Quality Policy
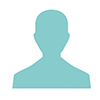
I have been asked by upper management to develop some type of policy to consistently address quality problems. We are a custom wireform manufacturer and are having increasing problems with "bad" parts being produced.
Does anyone have any type of policy that addresses this?
Does anyone have any type of policy that addresses this?
Comments
The standards we met came from past performance of the majority of employees. We sincerely felt that everyone we had on staff were capable of meeting the standards with a little effort, in other words we were not trying to eliminate anyone. So far it has worked well. At least one slacker has improved greatly, and now that the policy has been in place a few months, there is very little grumbling.
It seems like a starting point might be to look at some kind of average of past performance, and use cost analysis to determine the maximum waste allowed. I worked closely with the supervisors to determine the length of time, then after writing the policy I compared this timeline to a history of errors and speeds to see the effect. We made a few adjustments before printing. Our goal was to encourage a few stragglers to work harder, but not to get rid of anyone. Although we realized that might have been the result if it had not been successful.
Next I would like to work up some kind of reward system to encourage high speeds without errors...
The problem I have for this issue is that when "bad" parts are run they are typically unable to be used so they are considered "scrap". The amounts of scrap are getting just too high. This is typically a result of the employee not watching their machine and not doing their quality checks like they are supposed to.
One of the concerns voice by a supervisor is that they fear we may lose some "good" operators if we employ the progressive discipline for this issue. I explained to the supervisor that if they are consistently running scrap parts, they are not a "good" operator to begin with.
It is not my intent to terminate anyone but there seems to be an increasing sense of complacency regarding this issue.
I'm wondering if you'd be willing to share your "quality policy" with
me also. Our policy section gets thicker and thicker and thicker and th......
THANX!
[email]hrdir@iximd.com[/email]
or FAX (410) 398-0128
"Sam"
I agree with your statement regarding quality being a process but we are at the point that these employees are provided with training on the machines (extensive), they are also provided with a sample of what the part should be upon completion (this is approved through our Quality Manager) and they are provided with information regarding what, if any, tolerances there are for a particular job.
This situation is the result of employees simply failing to do the required quality checks as parts come off their machine and/or having a general attitude of complacency regarding their work.
So although I agree with your statement that quality is a process, I feel that at our organization we have the process in place and now we have to address the employees who fail to follow that process.
Lorrie - would you please email that policy to me as well? My email is [email]LindaS@Merrill-Mfg.com[/email].
Thank you.
While you're measuring each worker's scrap rate, you should also total the scrap rate for each supervisor's crew. If top brass is serious about this issue, they'll pressure the supervisors. If top brass doesn't hold supervisors' feet to the fire, then you'll know that this policy isn't worth a hill of beans.
James Sokolowski
HRhero.com